A CONCEPT FOR CONNECTING RODS
Optimized tools and tool paths enable higher cutting data and faster production of connecting rods.
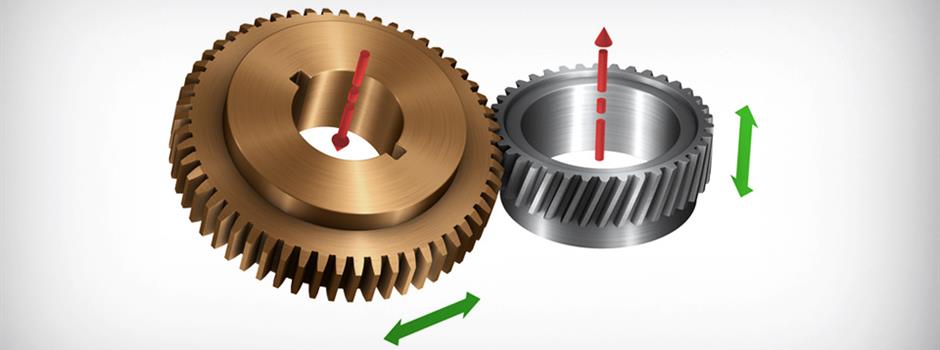
The internal combustion engine remains the near-term mainstay of automotive power, even as we are seeing emerging new technologies, such as electric vehicles and hydrogen power. The connecting rod is key component for converting the reciprocating power of pistons to rotational motion. As such, it needs to be light in weight to achieve optimal fuel efficiency and service life, yet the high reciprocal loads require maximum fatigue resistance. As with most automotive components, the manufacturing tolerances are very close.
The standard materials for connecting rods, the DIN C70 non-alloyed carbon steel in Europe and sintered materials in the United States, are straightforward in terms of machining. The key values that customers look for include minimal cost per component, secure processes and maximal performance in terms of output and machine utilization rate as well as component quality.
A mass-produced component, the connecting rod may warrant engineered or special tooling – for example drills or boring tools that combine roughing, finishing and chamfering into a single operation to maximize efficiency. Strong arguments for standard tools include faster availability and lower price.
Usually the most significant single cost component, however, is the cycle time. Optimized tools and tool paths enable higher cutting data and thus faster production.
Finish boring of the eyes
For the trucking industry or for larger size connecting rods, the CoroBore® 826 is Sandvik Coromant’s first choice for a fine boring tool for dedicated diameters and close hole tolerances (IT6).
The rigid and stable interface between the boring head and cartridge provides a firm basis for demanding finishing operations. The modular Coromant Capto® coupling system is the first choice for repeatability and stability, while its modularity also offers ease of use.
The HP system for high-precision coolant that is supplied directly to the cutting edge ensures excellent chip control. The chips are effectively broken up and evacuated out of the hole. This ensures that re-cutting of chips cannot jeopardize the highly repeatable, accurate process.
Innovative GC4300-series grades utilizing the Inveio™ technology provide excellent surface finish, reliability and process security. The TCEX L-F geometry should be chosen for best surface finish and highest productivity, while the –PF geometry optimizes chip breaking in steel. Wiper geometries can be used for optimizing the surface finish. Vibration risk can be countered by choosing a smaller nose radius.
Optimized round drills
Sandvik Coromant is launching new solid carbide drills optimized specifically for the operations on connecting rods. Particularly the entry stage of drilling has been challenging for standard round tools, and the new tools will provide a secure and productive solution to counter these problems.
A challenging component in terms of stability, the connecting rod calls for a highly secure drilling operation with maximum stability. The relatively deep bolt and oil holes require long overhangs and thus a strong drill and a stable coupling solution to counter vibration tendencies and maximize productivity. Chip removal can be problematic in deep holes. The inclined exit surfaces pose a challenge for conventional tools, as the resulting cutting forces easily result in a relatively short tool life.
The drill geometry must be sharp to minimize work hardening of the bore hole walls, which would seriously limit the tool life and process security during tap threading.
Sandvik Coromant’s solution will effectively counter the tool-life challenges posed by the component and will provide an excellent basis for the subsequent tapping operation.
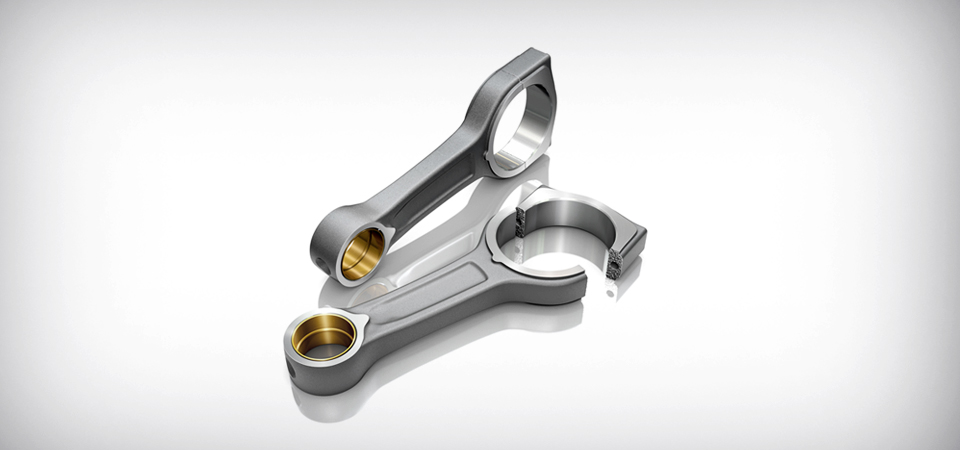
Cutting and forming taps
Sandvik Coromant is launching new solid carbide threading taps optimized for the bolt holes of connecting rods. The programme extension will start with cutting taps and will be complemented with forming taps.
The first choice for through holes, such as connecting-rod bolt holes, is the spiral point tap. These taps have a straight shallow flute and a gun nose or spiral point designed to drive the swarf forward. The relatively shallow flutes maximize the sectional strength of the tap and help the lubricant to reach the cutting edges.
An alternative to the conventional cutting tap is the cold forming tap, which produces the thread by means of plastic deformation rather than by the traditional cutting action. This has the advantage of eliminating swarf altogether.